5052 Aluminum Coil
5052 Aluminum Coil
Applications: Fuel Tank, Oil Pipe, Car Wheel Hub, Hood, Body Skin, Skeleton, Cabin Decoration, Curtain Wall, Ceiling, Battery Housing, Beverage Cans, Food Boxes, Pump Body, Valves, Precision Mechanical Workpiece, Mold Manufacturing, Etc.
Width: 100-2650mm | ||
Thickness: 0.2-10mm | ||
Length: Customizable as required | ||
Temper: F, O, H12, H14, H16, H18, H22, H24, H26, H28, H32, H34, H36, H38, etc. | ||
Mother Coil: DC or CC Aluminum Coil | ||
Surface: Oxidation, Precoating, Mirror Finishing, etc. | ||
Free Sample Size: A4 Paper Size | ||
MOQ: 3-5T | ||
Payment Terms: T/T, L/C, D/P | ||
Delivery Time: Normally Within 15-30 Days |
When introducing the 5052 aluminum coil, its advantages and characteristics cannot be ignored. It is an Al-Mg alloy material based on aluminum, which is lightweight, has high ductility, and has good electrical and thermal conductivity. The addition of magnesium significantly improves the alloy’s strength and corrosion resistance and also helps to improve its fatigue resistance.
A small amount of chromium enhances the hardness and corrosion resistance of the alloy by refining the matrix structure.
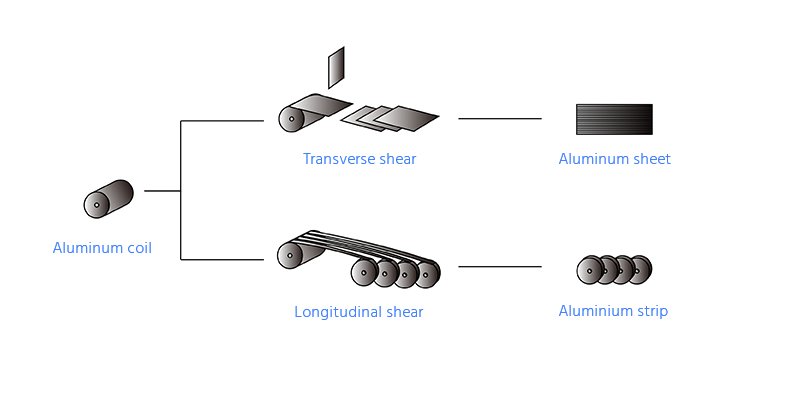
More importantly, the 5052 aluminum coil, with the anti-rust characteristics of 3-series aluminum alloy and the excellent forming and processing properties of 5-series alloy, is a high-quality material widely used in many fields, making it a rare and valuable aluminum alloy. In addition, the 5052 aluminum coil’s polishability also enhances its surface treatment, making it suitable for a variety of high-end application scenarios. These advantages and characteristics make 5052 aluminum coils a reliable and popular choice among many metal materials, with widespread use in various fields.
5052 aluminum coil properties
5052 Aluminum Coil Property | Value |
---|---|
Length | Customizable As Required |
Width | 100mm-2650mm |
Thickness | 0.2mm-10mm |
Temper | F, O, H12, H14, H16, H18, H22, H24, H26, H28, H32, H34, H36, H38, Etc. |
Application Market | Fuel Tank, Oil Pipe, Car Wheel Hub, Hood, Body Skin, Skeleton, Cabin Decoration, Curtain Wall, Ceiling, Battery Housing, Beverage Cans, Food Boxes, Pump Body, Valves, Precision Mechanical Workpiece, Mold Manufacturing, Etc. |
Surface | Oxidation, Precoating, Mirror Finishing, Etc. |
Free Sample Size | A4 Paper Size |
MOQ | 3-5T |
Delivery Time | Normally Within 15-30Days |
The 5052 aluminum coil produced by Wantai has various alloy states, including O, F, H12 to H38, and others. The thickness ranges from 0.2mm to 10mm, the widths from 100mm to 2650mm, and the lengths can be determined according to specific order requirements. Our 5052 aluminum coil has excellent mechanical properties, dimensional accuracy, and low error fluctuations, which can meet various high-precision machining needs and is very suitable for customers with strict material properties requirements.
Al-Mg2 5251 Aluminum Alloy Chemical Composition
The 5052 aluminum coil, a representative of an Al-Mg alloy aluminum material, has a chemical composition that’s been carefully balanced to achieve optimal performance. The main elements and their contents are as follows:
AlMg2 Aluminum Physical Property
The 5052 aluminum alloy sheet performs well in terms of physical properties and is the first choice for lightweight materials. The 5052 aluminum alloy sheet is more than lightweight. It’s also highly efficient in heat dissipation and electrical conductivity, ensuring top-notch performance in applications requiring efficient heat exchange or electrical conduction.
AlMg2 Aluminum Mechanical Property
Regarding mechanical properties, the 5052 aluminum alloy plate shows high strength and excellent flexibility. Good machining performance allows it to withstand greater external force and absorb impact energy to a certain extent, guaranteeing the structure’s safety.
Fabrication Property
When it comes to processing performance, the 5052 aluminum coil is a dream to work with. Its moderate hardness and excellent cold processing performance make it easy to cut, bend, weld, and treat surfaces. It’s a versatile material that can meet the processing needs of even the most complex parts, giving you the confidence to tackle any project.
Moreover, the 5052 aluminum coil offers many possibilities with its diverse and flexible surface treatment options. From anodizing to electroplating, polishing to painting, and other processes, these varied treatments can give products a wide range of appearances and performance characteristics, providing exciting customization options. For example, the surface color-coated polyester coating (PE) and fluorocarbon coating (PVDF) have bright colors and strong adhesion and significantly improve the product’s corrosion and weather resistance. In addition, the mirror color coated aluminum coil, through rolling, polishing, and other processes, the surface of the plate to achieve the mirror effect, and then with the roller coloring technology, can form a variety of gorgeous colors, widely used in the field of decoration.
Advanced Color-Coated Process
Polyester-Coated Pre-Coating Technology (PE Coating)
The polyester coating is an anti-UV UV polyester resin coating; its primary component uses polymers containing ester bonds in the main chain as monomers, adding alkyd resin and an ultraviolet absorber. After baking polyester coating on the surface of aluminum (aluminum sheet, aluminum coil) many times, it forms a solid film with protection and decoration. The polyester coating protects color-coated aluminum products (aluminum sheets, aluminum coils) from exposure to the atmosphere due to temperature differences, freeze-thaw cycles, corrosive gases and microorganisms, ultraviolet radiation, wind, rain, frost, and snow.
Furthermore, the polyester coating is a powerful tool for enhancing the visual appeal of aluminum substrate products. It offers a rich color palette for color-coated aluminum products, and depending on the desired gloss, the polyester coating can be divided into matte and highlight series. This aesthetic enhancement ensures that the color-coated aluminum coil not only has good gloss and smoothness but also superior texture and feel, increasing the sense of layer and three-dimensionality. Its ability to enhance the visual appeal makes it a perfect fit for interior decoration and advertising boards.
Polyvinylidene Difluoride Coating Technology (PVDF Coating)
Fluorocarbon coating is PVDF resin. It mainly refers to vinylidene fluoride homopolymer or vinylidene fluoride and other small amounts of fluorinated vinyl monomer copolymer coatings. The fluoric acid-base material with a fluorine/carbonization bond has a stable and firm chemical structure, which makes the physical properties of fluorocarbon coatings different from those of general coatings.
Fluorocarbon coatings can be divided into traditional fluorocarbon coatings and nano-fluorocarbon coatings according to the film formation structure of the surface. In 1965, the Pennwalt Chemical Company of the United States, for the first time, used fluorocarbon paint for the coating of indoor and outdoor aluminum in high-grade buildings. A wide range of color selectivity, solemn appearance, and durability added luster to many magnificent curtain wall buildings around the world.
Fluorocarbon coatings, in addition to their mechanical properties of wear and impact resistance, demonstrate exceptional long-term fading and UV resistance in harsh climates and humid environments. After high-temperature grilling, the molecular structure of the coating becomes tight, ensuring superior weather resistance. The manufacturer’s guarantee of the service life of the coating has been extended from 10 years to 15 years, and now even exceeds 20 years, providing a secure and long-lasting investment.
Fluorocarbon coatings have been extensively tested and compared with super and general coatings by American research institutions. The samples of the coatings were exposed to hot sunlight in Florida, the United States, and to the harsh environment of humid salty air for 12 years. This rigorous testing proves that the stability and durability of fluorocarbon coatings are 30%-80% higher than those of the other two coatings, providing reassurance about their reliability. Fluorocarbon coatings are a dependable choice for various harsh environments, especially for indoor and outdoor decoration in public places, commercial chains, exhibition advertising, and other decorations and displays.
Anti-corrosion Property
Because of the presence of magnesium in its composition, the 5052 aluminum coil can effectively block the erosion of various corrosive media, including acid, alkali, salt, and other corrosive environment. Therefore, the 5052 alloy aluminum coil has naturally good corrosion resistance and is widely used in various corrosive environments, especially in Marine or chemical corrosion environments; its corrosion resistance is particularly prominent. Under exceptional circumstances, the corrosion resistance of 5052 aluminum coil is better than that of pure aluminum plate such as 1060 aluminum alloy. In addition, the 5052 aluminum coil can also further improve its corrosion resistance through anodizing and other surface treatment processes to ensure that it can maintain good performance in harsh environments such as Marine, chemical, and construction. This makes the 5052 aluminum coil ideal for ships, automobiles, chemical equipment, and other fields.
Environmental Protection and Recyclability
5052 aluminum coil is an environmentally friendly metal material, with relatively little waste generated during production and processing. At the same time, aluminum has good recyclability and can realize the recycling of resources. This helps to reduce environmental pollution and waste of resources.
In general, 5052 aluminum coil with its unique chemical composition, excellent physical properties, excellent mechanical properties, diversified processing properties, excellent corrosion resistance, and good welding performance, as well as beautiful and durable characteristics, in aerospace, automotive, shipbuilding, construction, electronic products, and other fields have shown a wide range of application prospects. As a professional sales staff, we know the importance of product quality, whether it is the pursuit of lightweight, high-strength aerospace field or the building decoration industry with strict requirements for beauty and corrosion resistance. We will happily provide customers with high-quality, excellent 5052 aluminum coil and professional technical support. Welcome to inquire.
Differences Between DC Casting And CC Casting
The thickness of 0.7 mm refers to the thickness of aluminum coils, commonly used in various industries for roofing, cladding, and fabrication applications. So, comparing the quality of aluminum coils with a 0.7 mm thickness through some details on DC and CC Casting could help us get a clear and reasonable result.
DC (Direct Chill) Casting
- The direct chill casting process produces a magnificent and uniform aluminum grain structure.
- This fine-grain structure gives aluminum strength, formability, and corrosion resistance compared to other casting methods.
- Direct chill-casting aluminum coils are often used in applications that require deep drawing or complex forming, such as automotive body panels, heat exchangers, and food/beverage cans.
- The 0.7 mm thickness is on the thinner end for DC casting aluminum. However, this gauge is still suitable for many formed and fabricated components.
CC casting (Continuous Casting)
- Continuous Casting is a more economical process than DC casting.
- CC-casting aluminum billets, blooms, or slabs have a slightly larger grain structure than DC-casting. However, it is still suitable for a wide range of applications.
- CC-casting aluminum coils with a thickness of 0.7 mm are commonly used for general sheet metal fabrication, roofing, siding, and other building/construction applications.
- The 0.7 mm thickness provides a good balance of formability, strength, and lightweight properties for these types of uses.
In summary, DC-casting aluminum coils have superior mechanical properties and surface quality compared to CC-casting but at a slightly higher cost. Even so, neither DC nor CC-casting aluminum coils with a thickness of 0.7 mm can exhibit good flatness, surface quality, and dimensional tolerance and can be used in different applications depending on the project’s specific requirements.
The choice between the two kinds of production technology depends on the end product’s specific performance requirements, economic considerations for the specific application, and customer requirements. DC casting is preferred when superior formability and strength are needed. In contrast, CC casting is more economical for less demanding applications.
We provide all the data from authoritative third-party testing agencies, including AQSIQ, the International Organization for Standardization, etc. These institutions have comprehensively evaluated the performance of 3105 aluminum coils through strict test methods and evaluation standards. Customers can inquire about the relevant report or contact us for more detailed information.
5052 Aluminum Coil Chemical Composition
The 5052 aluminum coil, sheet, and foil parameters are similar or identical to those of the International Alloy Designations System for 5251 Aluminum Alloy.
Chemical Element | Si | Fe | Cu | Mn | Mg | Cr | Ni | Zn | V | Ga | Ti | Zr | Each | Total | Al |
---|---|---|---|---|---|---|---|---|---|---|---|---|---|---|---|
Content (%) | ≤0.25 | ≤0.40 | ≤0.10 | 0.10 | 2.20-2.80 | 0.15-0.35 | – | 0.10 | – | – | – | – | ≤0.05 | ≤0.15 | Remainder |
AlMg2 Aluminum Coil Technical Data
Length | Customizable As Required |
Width | 100-2650mm |
Thickness | 0.2-10mm |
Temper | F, O, H12, H14, H16, H18, H22, H24, H26, H28, H32, H34, H36, H38, Etc. |
Application Market | Fuel Tank, Oil Pipe, Car Wheel Hub, Hood, Body Skin, Skeleton, Cabin Decoration, Curtain Wall, Ceiling, Battery Housing, Beverage Cans, Food Boxes, Pump Body, Valves, Precision Mechanical Workpiece, Mold Manufacturing, Etc. |
Mother Coil | DC or CC Aluminum Coil |
Surface | Oxidation, Precoating, Mirror Finishing, Etc. |
Free Sample Size | A4 Paper Size |
MOQ | 3-5T |
Payment Terms | T/T, L/C, D/P |
Delivery Time | Normally Within 15-30 Days |
5052 aluminum coil properties
Physical Property | Value |
---|---|
Density | 2.69g/cm3 |
Hardness Brinell | 20-30HB |
Melting Point | 625°C |
Thermal Expansion | 24 x10^-6 /°C |
Thermal Conductivity | 134W/m.K |
Electrical Resistivity | 0.044 x10^-6 Ω.m |
Mechanical Property | Value |
---|---|
Tensile Strength | ≥165 MPa |
Compressive Strength | ≥210MPa |
Yield Strength | ≥110MPa |
Shear Strength | ≥125 MPa |
Modulus of Elasticity | ≥70Gpa |
Elongation | ≥5% |
Elongation at Break | ≥2.3% |
5052 Aluminum Coil DC / CC Temper designation (For Reference)
Temper | Definition |
---|---|
O | Soft |
H12 | Strain Hardened, 1/4 Hard |
H14 | Strain Hardened, 1/2 Hard |
H16 | Strain Hardened, 3/4 Hard |
H18 | Strain Hardened, Full Hard |
H22 | Strain Hardened and Partially Annealed, 1/4 Hard |
H24 | Strain Hardened and Partially Annealed, 1/2 Hard |
H26 | Strain Hardened and Partially Annealed, 3/4 Hard |
H28 | Strain Hardened and Partially Annealed, Full Hard |
5052 aluminum coil Corrosion resistance
The corrosion resistance of 5052 aluminum coil in acid and alkali is roughly as follows
Medium | Anti-corrosion Capability |
---|---|
Ocean Water | weak |
Salt | weak |
Organic Acid | Common |
fluorine, chlorine, bromine, Lodine | Poor |
hydrochloric acid, hydrofluoric acid, acetic acid | Poor |
alkaline, ammonia water, Lime water | Poor |
dilute sulfuric acid, dilute nitric acid | Poor |
ammonia Gas, sulfurous gas | Good |
Cold concentrated sulfuric acid, Cold concentrated nitric acid | Stable |
petroleum, kerosene, ethyl alcohol, benzene, organic compound, etc | Stable |
5052 Aluminum Coil Applications
5052 aluminum coil, with its unique chemical composition, excellent physical and mechanical properties, diversified processing properties, excellent corrosion resistance, good welding performance, and beautiful and durable characteristics, shows a wide range of application prospects in aerospace, automotive, shipbuilding, construction, electronic products, and other fields. Whether in the aerospace field, which pursues lightweight and high strength, or in the architectural decoration industry, which demands strict aesthetics and corrosion resistance, the 5052 aluminum coil has certain advantages and limitations. We should be fully aware of the potential characteristics of EN AW-5251 aluminum alloy to exploit the benefits and avoid the disadvantages in the corresponding application scenarios. Reduce unnecessary trouble and loss.
Advantages
- Lightweight
Compared to other metal materials, the 5052 aluminum coil has a lower density and higher strength, which helps to provide significant advantages in application scenarios requiring weight reduction and energy efficiency, such as aerospace, automotive manufacturing, and other fields. - Excellent Corrosion Resistance
5052 aluminum coil is an Al-Mg alloy with an appropriate amount of magnesium. It has good corrosion resistance, can maintain its stable performance in harsh environments, and cannot quickly oxidize or corrode. This feature is particularly suitable for applications that require prolonged exposure to humid, corrosive environments. - Good Processing Performance
The alloy material has good plasticity, ductility, and weldability and is easy to carry out various cold working operations, such as stamping, bending, stretching, etc. At the same time, good welding performance can be connected by multiple welding methods to meet complex and diverse shape and size manufacturing needs. - Moderate Strength and Hardness
Tensile strength (σb): 170 ~ 340MPa, yield strength (σ0.2) : ≥65MPa (some data indicate ≥90MPa), the specific values are affected by the machining thickness, alloy state (such as H32, H34, etc.) and processing conditions. Hardness: 45 ~ 76HB. The medium hardness makes the 5052 aluminum coil maintain a certain hardness simultaneously. Still, it also has a high strength, can meet the requirements of many structural parts for material strength, and is easy to process. It can also withstand a particular load and is not easily deformed or damaged. - Excellent Surface Treatment Ability
The alloy material can efficiently perform surface treatment, such as anodizing, spraying, etc. The 5052 aluminum coil can be endowed with rich color and texture through these processing processes, improving its beauty, durability, and added value. At the same time, the surface treatment can further enhance its corrosion and wear resistance. - Good Formability
The 5052 aluminum coil shows good formability during molding and can be quickly processed into various complex shapes and sizes. This property makes it a significant advantage in manufacturing complex structural parts. - Wide Range of Applications
Due to its excellent performance and various processing methods, the 5052 aluminum coil is widely used in transportation, architectural decoration, electronic appliances, packaging containers, and other fields. It can meet the diverse needs of different industries for material properties. - Environmentally Friendly and Recyclable
Aluminum itself is an environmentally friendly and recyclable metal resource. 5052 aluminum coil can be well recycled during and after waste and will not pollute the environment. This aligns with the concept of modern society’s environment and the requirements for concept and sustainableinquirements.
As a widely used aluminum alloy, 5052 aluminum coil has many advantages, such as excellent corrosion resistance, good processing performance, moderate strength and hardness, excellent surface treatment ability, good formability, environmental protection recyclability, and a wide range of application fields. It has shown strong application potential and market value in many industries. But there are some disadvantages and limitations. The following is a detailed analysis of its disadvantages and limitations:
Disadvantages
- Poor Machinable Performance
Due to the influence of its material characteristics, the 5052 aluminum coil cutting process could improve cutting performance. This can lead to reduced processing efficiency and increased cutting tool wear, and the machined surface quality could be better than that of some other aluminum alloy materials. - The Heat Treatment Strengthening Effect Is Not Good
5052 aluminum coils cannot be significantly strengthened by heat treatment. This means that where high-strength applications are required, other aluminum alloy materials that can be strengthened by heat treatment may need to be selected. - Surface Defects
In the production and processing process, 5052 aluminum coil may appear a variety of surface defects, such as splintering, collapse, side bending, waves, embossing, abrasion, warping, corrosion, surface oil, scratches, surface black spots, etc. These defects may affect the product’s appearance, quality, and performance. - Low Airtightness
Although the 5052 aluminum coil weld has high strength and plasticity, its air tightness is relatively low. This may lead to the need to take additional measures to improve the tightness of welds in certain situations where high air tightness is required, such as aerospace, pressure vessels, and other fields.
Limitations
- Application Field Limitations
Although 5052 aluminum coil has a wide range of applications in many fields, due to its poor machinability, poor heat treatment strengthening effect, and other shortcomings, it may not be the best choice in some instances where machining performance and strength requirements are incredibly high. - Consideration of Material Cost
5052 aluminum coils may cost more than other aluminum alloy materials.
This may limit its use in some cost-sensitive applications. - Increase in Processing Difficulty
Because the 5052 aluminum coil is prone to surface defects and poor cutting performance during processing, it may increase the difficulty and cost of processing. Therefore, these factors must be considered when designing and selecting the processing process.
In summary, although the 5052 aluminum coil has many advantages, its shortcomings and limitations must also be considered in the application process. Careful consideration and balance should be made according to specific application scenarios and requirements when selecting and using it.
Aerospace Industry
5052 aluminum coil is also widely used in the aerospace industry; its high strength, fatigue resistance, and corrosion resistance ensure the safe operation of aircraft in extreme environments. Therefore, 5052 aluminum is mainly used to manufacture aircraft shells, wing spars, landing gear, and other vital structural parts. Its lightweight, high-strength, and corrosion-resistant properties help reduce the aircraft’s overall weight and improve flight performance and fuel efficiency. According to industry reports, aircraft parts made of 5052 aluminum can reduce weight by about 15% compared to traditional materials, significantly improving flight economy.
- Aerospace: fuselage skin, skeleton, cabin decoration, bulkhead, wing SPAR, and other structural parts.
Architectural Decoration and Building Materials: The Perfect Combination of Architectural Aesthetics and Practicality
In modern architecture, the 5052 aluminum coil adds beauty and texture to the building in construction because of its good surface treatment performance, formability, and rich color choices. Various visual effects can be presented through anodizing, spraying, and other processing processes to improve the beauty and overall quality of the building. In addition, its corrosion resistance and lightweight characteristics also meet the high requirements for material performance in modern buildings. They are widely used in facade decoration and internal structures such as curtain walls, ceilings, roofs, doors, and Windows.
- Curtain Wall: 5052 aluminum coils are often used to make curtain walls and ceilings in modern buildings due to their excellent machinability and surface treatment capabilities. Through anodizing, spraying, and other processes, rich colors and textures can be presented to enhance the building’s aesthetics and durability.
- Roofing Materials: In some high-end residential and commercial buildings, 5052 aluminum coils are also used. These coils are favored for their light weight, corrosion resistance, and easy maintenance. 5052 aluminum coils also play an essential role in the interior decoration of commercial buildings, airports, high-speed rail/stations, subways, and other public places. Because of its diverse surface treatment methods (such as oxidation and spraying), it has created a colorful color and texture appearance and flexible combination of needs, making it able to meet the decorative style needs of different places.
Packaging Materials: Innovative Applications in the Packaging Industry
In the food, beverage, and cosmetics industries, the choice of packaging materials is directly related to the quality and safety of the product. EN AW-5251 aluminum coil has become the ideal choice of packaging material for these industries because of its non-toxic, tasteless, and corrosion-resistant properties. Therefore, in the production of cake trays, candle holders, and tea cans, 5052 aluminum coils not only maintain the shape and beauty of the product but also ensure its health and safety during transportation and storage.
With the enhancement of consciousness of property rights and security, the anti-counterfeiting of wine has also received increasing attention. First, the bottle cap made of 5052 aluminum alloy can print colorful patterns, which can be filled with anti-counterfeiting marks and improve the product’s overall quality and market competitiveness. Secondly, the 5052 aluminum alloy bottle cap has a smooth surface and excellent sealing, but it also prevents the leakage of liquid content. In addition, the excellent processing performance of EN AW-5251 aluminum alloy bottle caps makes it easy to achieve mass production and low production costs, which can also help users save a lot of costs. What is more noteworthy is that its recyclability is also in line with modern environmental protection concepts, promoting the development of green packaging.
- Food Packaging: Due to their non-toxic and corrosion-resistant characteristics, 5052 aluminum coils, such as beverage cans and food boxes, are also widely used in food packaging.
- Chemical Packaging: For chemical packaging that requires acid and alkali corrosion resistance, 5052 aluminum coils perform well and can effectively protect the contents from the external environment.
Automobile Industry: Lightweight, Energy Saving and Emission Reduction
In the automotive industry, 5052 aluminum coils are widely used to manufacture fuel tanks, body panels, and other components. Their excellent corrosion resistance effectively resists the erosion of chemical substances such as gasoline and extends the tank’s service life. At the same time, the material’s excellent weldability makes it easy to process and connect in the body manufacturing process, improving production efficiency. According to the automobile manufacturer’s feedback, body parts made of 5052 aluminum can reduce the weight of the vehicle by more than 30% compared to traditional steel parts while improving its fuel efficiency.
- Body and Parts: The EN AW-5251 aluminum coil is widely used in automobile manufacturing to manufacture the body structure, chassis, fuel tank, oil pipe, car hub, hood, trunk lid, and other unique parts for transportation equipment, because of its good formability and corrosion resistance. Its lightweight nature helps to reduce body weight and improve fuel efficiency.
Electronic and Electrical Product Industry
The 5052 aluminum coil is an indispensable material for manufacturing battery housing, radiators, shells, and other components in the electronic and electrical industry. The high corrosion resistance and excellent thermal conductivity of 5052 aluminum alloy ensure the stability and reliability of electronic products. At the same time, the exemplary processing properties make 5052 aluminum easy to form and process in the manufacturing process of electronic and electrical products.
- Heat Sink and Shell: The heat sink and shell of high-end air conditioning shells and electronic equipment are often made of 5052 aluminum coil, which uses its excellent thermal conductivity and corrosion resistance to ensure the equipment’s stable operation and long life.
- Battery Housing: 5052 aluminum coils are used to manufacture battery housing in new energy vehicles and storage systems. Their strength and corrosion resistance ensures the safety and reliability of the battery pack. Because of their excellent metal texture, wear resistance, and corrosion resistance, 5052 aluminum coils are favored in 3C products such as mobile phones, laptops, and tablets.
Mechanical Equipment and Piping System
In mechanical equipment manufacturing, 5052 aluminum coils are used to manufacture parts requiring certain strength and antimicrobial resistance, such as pump bodies, valves, automatic mechanical parts, precision mechanical workpieces, molds, etc.
In the pipeline system, especially in fields that require corrosion resistance, such as seawater desalination, chemical treatment, and others, the 5052 aluminum coil pipeline shows its unique advantages.
Other Industrial Applications
In addition, 5052 aluminum coils are widely used in shipbuilding, chemical equipment, and other fields. Its excellent performance and diverse specifications enable 5052 aluminum to meet the diverse needs of different industries for material properties.
It is not difficult to see from the above many applications that the 5052 alloy EN AW-5251 aluminum coil, with its lightweight, high strength, high corrosion resistance, high thermal conductivity, easy processing, excellent electrical conductivity, environmental protection and recycling, and other excellent performance characteristics, has been widely used in many fields. With the progress of science and technology and the continuous market expansion, the application prospect of the 5052 aluminum coil will be broader.
Lastly, we offer flexible, customized services to produce EN AW-5251 AlMg2 aluminum coils of different sizes, thicknesses, surface treatments, and performance requirements according to our customers’ needs. At the same time, we provide professional technical support and after-sales service to ensure that customers get timely technical support and solutions during the use process.Please feel free to contact us for orders.
WanTai Aluminum Industry Product List
Aluminum Alloy Series | Aluminum Grade |
---|---|
1000 Series | 1050, 1060, 1070, 1100, etc. |
2000 Series | 2014, 2017, 2024, 2A11, 2A12, 2A14, etc. |
3000 Series | 3003, 3004, 3005, 3104, 3105, 3A12, etc. |
4000 Series | 4004, 4032, 4043, 4047, 4A03, 4A11, 4A13, 4A17, etc. |
5000 Series | 5005, 5052, 5052A, 5052B, 5059, 5083, 5086, 5182, 5252, 5454, 5754, 5A02, 5A03, 5A05, 5A06, 5M49, 5M52, etc. |
6000 Series | 6005, 6005A, 6060, 6061, 6063, 6082, 6101, etc. |
7000 Series | 7005, 7050, 7075, 7A04, 7A09, etc. |
8000 Series | 8011, 8076, 8077, 8079, 8176, 8177, 8276, 8280, etc. |
Types | Aluminum Coils, Aluminum sheets, Aluminum foils, Aluminum strips, Checkered Plates or diamond plates, etc. |
Length(mm) | customizable as required. |
Width(mm) | 40mm-2650mm |
Thickness(mm) | 0.006mm-800mm |
surface | oxidation, Precoating, wire drawing, Mirror Finishing, embossing, etc. |
payment | T/T, L/C, D/P, etc. |
package | Wrap in plastic or kraft paper with Moisture-proof desiccant. Pack in fumigated wooden cases and brackets. |
Different Specifications of Aluminum Coil Parameters
The following are examples of different specifications of aluminum rolls and their weight and length information for Reference:
specification | Thickness(M) | Area(m2) | Weight(Kg) |
---|---|---|---|
0.5mmx1mx1000m | 0.0005 | 1000 | 1,350 |
0.6mmx1mx1000m | 0.0006 | 1000 | 1,620 |
0.8mmx1mx1000m | 0.0008 | 1000 | 2,160 |
1.0mmx1mx1000m | 0.0010 | 1000 | 2,700 |
1.5mmx1mx1000m | 0.0015 | 1000 | 4,050 |
2.0mmx1mx1000m | 0.0020 | 1000 | 5,400 |
2.5mmx1mx1000m | 0.0025 | 1000 | 6,750 |
3.0mmx1mx1000m | 0.0030 | 1000 | 8,100 |
Interested In Working With WANTAI?
Please insert your contact information into the following contact form and let us know how we can help you! We will contact you as quickly as possible.
People Also Searched for 3003 Aluminum Coil
Aluminum Coil Uses, Aluminum Coil Exporter In China, Aluminum Coil Price In India, Aluminum Coil, Aluminum Coil Price Per Kg, Aluminum Coil Hs Code, Aluminum Coil Supplier In Delhi, 3003 Aluminum Coils Suppliers, CC Casting Aluminum Coil, Al 3003 Coil, Aluminum Alloy 3003 Coils Stockholders, Aluminum 3003 Coils Exporters, Aluminum 3003 Coils Manufacturers, Aluminum Alloy 3003 Coil Size, Aluminum Alloy 3003 Slitting Coil, Aluminum Alloy 3003 Coils Price List India, 3003 Aluminum Coils, Al Alloy 3003 Coil, Aluminum 3003 Coils, 3003 Aluminum Coil Distributors, Aluminum Alloy 3003 Coils, Aluminum Coils Suppliers, Aluminum Alloy 3003 Coil Supplier, Aluminum 3003 Coils Exporters, Aluminum 3003 Slitting Coil Manufacturers, Aluminum Alloy 3003 Coil Price, Aluminum Alloy 3003 Coils Distributors, Aluminum Alloy 3003 Coil, Aluminum Alloy 3003 Coils Stock, Aluminum 3003 Coil Exporter, 3003 Aluminum Coil price, 3003 Aluminum Coil size, 3003 Aluminum Coil for sale, Aluminum 3003 chemical composition, 3003 H14 Aluminum, etc.