1060 Aluminum Coil
1060 Aluminum Coil
Application Market: Connection of Power Battery, Aluminum-Plastic Panel, Lamp Material, Capacitor Shell, Road Sign, Building Exterior Wall, etc.
Width: 40-2650mm | ||
Thickness: 0.2-5mm | ||
Length: Customizable as required | ||
Mother Coil: DC or CC | ||
Temper: O, H12, H14, H16, H18, H22, H24, H26, H28, etc. | ||
Surface: Oxidation, Precoating, Mirror Finishing, Checkered or Diamond, etc. | ||
Free Sample Size: A4 Paper Size | ||
MOQ: 3T | ||
Payment Terms: T/T, L/C, D/P | ||
Delivery Time: Normally Within 15-30Days |
An aluminum coil is a rolled metal product calendered by a finishing mill and processed by drawing and bending angles without smooth flying shear. It is the raw material of aluminum strips and plates. The slitting equipment can cut the aluminum roll into strips, and the flattening equipment can make the aluminum roll into a sheet.
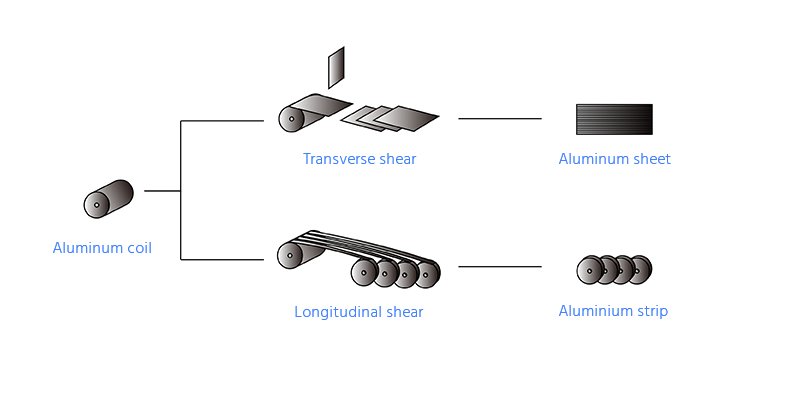
1060 Aluminum Coil DC / CC International Alloy designation (For Reference)
The parameters of the 1060 aluminum coil and pre-painted 1060 aluminum coil are identical to those of the International Alloy Designations System for 1060 Aluminum sheets.
Alloy Series | National Standard | American Standard | Europe Standard |
---|---|---|---|
1000 Series | 1060 Aluminum Coil | 1060 Aluminum Coil | – |
1060 Aluminum Coil Dimension Property | Value |
---|---|
Length | Customizable As Required |
Width | 100mm-2650mm |
Thickness | 0.2mm-5mm |
1060 aluminum coil, which belongs to industrial aluminum, is also the highest aluminum alloy in the 1000 series aluminum coil, with an aluminum content of more than 99.60%. In essence, it is very similar to 1050 aluminum alloy. The difference is that the aluminum content is different. Therefore, the chemical composition and physical properties of the 1050 aluminum coil and 1060 aluminum coil are almost similar. They can replace each other. 1060 aluminum coil stands out as the most widely used product in the market. Its key advantage lies in its straightforward production process, mature technology, and notably competitive price compared to other high-grade aluminum alloys.
1060 aluminum alloy has good ductility, high plasticity, and formability. Although it has low strength and can not be strengthened by heat treatment, it can fully meet the requirements of conventional stamping and drawing processing as a deformation alloy. 1060 aluminum alloy is highly flexible and can withstand various pressures, stretching, and bending. Therefore, the 1060 aluminum coil is usually made by extrusion or rolling.
The Wantai 1060 aluminum coil production has caught up with developed countries. We provide 1060 aluminum coil surface flat, high cleanliness, strong weldability, suitable for polymer welding. In addition, the 1060 aluminum coil also accepts gas welding, arc welding, hydrogen atom welding, contact spot welding, and wire welding, but it takes work to braze. Widely used in building appearance decoration, high-rise and factory wall decoration, bus bodies, welding parts, nameplates, clock surfaces, disks, reflective equipment, lamps, signs, and other fields.
1060 aluminum coil boasts high corrosion resistance and exceptional electrical and thermal conductivity, making it a versatile choice. It finds applications in electronic and electrical, petrochemical, and packaging industries. For instance, it’s ideal for chemical instruments, battery bus soft connections, capacitors, vacuum tube isolation nets, wire and cable protective sleeves, heat exchangers, aircraft ventilation system parts, and decorative parts. In addition, 1060 aluminum alloy has high elongation and high flexibility. It is widely used in deep-drawing or spinning concave utensils, kitchenware, aluminum gaskets, lamp shades and lamp holders, kitchen sinks, lamp holders, fan blades, and other industries.
Components of 1060 Aluminum Coil
Chemical composition | Content(%) |
---|---|
Si | ≤0.25 |
Cu | ≤0.05 |
Mg | ≤0.03 |
Zn | ≤0.05 |
Mn | ≤0.03 |
Ti | ≤0.03 |
V | ≤0.05 |
Fe | ≤0.35 |
Al | ≥99.60 |
WanTai Aluminum is happy to provide you with various aluminum coils, such as color-coated aluminum coils, checkered aluminum coils, and white aluminum sheet trim rolls. Please contact our professional sales butler team if you have any requests.
1050 Aluminum Coil DC / CC Temper designation (For Reference)
Temper | Definition |
---|---|
O | Annealed |
H12 | Strain Hardened, 1/4 Hard |
H14 | Strain Hardened, 1/2 Hard |
H16 | Strain Hardened, 3/4 Hard |
H18 | Strain Hardened, Full Hard |
H22 | Strain Hardened and Partially Annealed, 1/4 Hard |
H24 | Strain Hardened and Partially Annealed, 1/2 Hard |
H26 | Strain Hardened and Partially Annealed, 3/4 Hard |
H28 | Strain Hardened and Partially Annealed, Full Hard |
Differences between DC Casting and CC Casting
The thickness of 0.7 mm refers to the thickness of aluminum coils, commonly used in various industries for roofing, cladding, and fabrication applications. So, comparing the quality of aluminum coils with a 0.7 mm thickness through some details on DC and CC Casting could help us get a clear and reasonable result.
DC (Direct Chill) Casting:
- The direct chill casting process produces a magnificent and uniform aluminum grain structure.
- Compared to other casting methods, this fine-grain structure gives aluminum strength, formability, and corrosion resistance.
- Direct chill-casting aluminum coils are often used in applications that require deep drawing or complex forming, such as automotive body panels, heat exchangers, and food/beverage cans.
- The 0.7 mm thickness is on the thinner end for DC casting aluminum. However, this gauge is still suitable for many formed and fabricated components.
CC casting (Continuous Casting):
- Continuous Casting is a more economical process than DC casting.
- CC-casting aluminum billets, blooms, or slabs have a slightly larger grain structure than DC-casting. However, it is still suitable for a wide range of applications.
- CC-casting aluminum coils with a thickness of 0.7 mm are commonly used for general sheet metal fabrication, roofing, siding, and other building/construction applications.
- The 0.7 mm thickness provides a good balance of formability, strength, and lightweight properties for these types of uses.
In summary, DC-casting aluminum coils have superior mechanical properties and surface quality compared to CC-casting but at a slightly higher cost. Even so, neither DC nor CC-casting aluminum coils with a thickness of 0.7 mm can exhibit good flatness, surface quality, and dimensional tolerance and can be used in different applications depending on the project’s specific requirements. The choice between the two kinds of production technology depends on the end product’s specific performance requirements, economic considerations for the specific application, and customer requirements. DC casting is preferred when superior formability and strength are needed. In contrast, CC casting is more economical for less demanding applications.
Advanced Color-Coated Process
Polyester-coated pre-coating Technology(PE Coating)
The polyester coating is a kind of anti-UV UV polyester resin coating; its primary component uses polymers containing ester bonds in the main chain as monomers, adding alkyd resin and an ultraviolet absorber. After baking polyester coating on the surface of aluminum (aluminum sheet, aluminum roll) many times, it forms a solid film with protection and decoration. The polyester coating protects color-coated aluminum products (aluminum sheets, aluminum rolls) from exposure to the atmosphere due to temperature differences, freeze-thaw cycles, corrosive gases and microorganisms, ultraviolet radiation, wind, rain, frost, and snow.
In addition, the polyester coating can give color-coated aluminum substrate products rich color. According to gloss, the polyester coating can be divided into matte and highlight series. Therefore, the color-coated aluminum coil not only has good gloss and smoothness but also superior texture and feel and can also increase the sense of layer and three-dimensionality. It is especially suitable for interior decoration and advertising boards.
polyvinylidene difluoride coating technology(PVDF Coating)
Fluorocarbon coating is PVDF resin. It mainly refers to vinylidene fluoride homopolymer or vinylidene fluoride and other small amounts of fluorinated vinyl monomer copolymer coatings. The fluoric acid-base material with a fluorine/carbonization bond has a stable and firm chemical structure, which makes the physical properties of fluorocarbon coatings different from those of general coatings.
Fluorocarbon coatings can be divided into traditional fluorocarbon coatings and nano-fluorocarbon coatings according to the film formation structure of the surface. In 1965, the Pennwalt Chemical Company of the United States, for the first time, used fluorocarbon paint for the coating of indoor and outdoor aluminum in high-grade buildings, a wide range of color selectivity, solemn appearance, and durability for many magnificent curtain wall buildings around the world added luster. In addition to the wear and impact resistance in terms of mechanical properties, it also shows excellent and long-term fading resistance and UV resistance in harsh climates and humid environments. After high-temperature grilling, the molecular structure of the coating is tight, and the machine has superior weather resistance. The coating manufacturer’s guarantee of the service life of the coating began to be 10 years, 15 years to guarantee more than 20 years.
American research institutions have tested and compared fluorocarbon, super, and general coatings. The samples of the coatings were exposed to hot sunlight in Florida, the United States, and exposed to the harsh environment of humid salty air for 12 years, which proves that the stability and durability of fluorocarbon coatings are 30%-80% higher than those of the other two coatings. Fluorocarbon coatings ensure that they can be used in various harsh environments. It is especially suitable for indoor and outdoor decoration in public places, commercial chains, exhibition advertising, and other decorations and displays.
Due to the simple production process of 1000 series alloy coils, such as 1050 aluminum coils, 1060 aluminum coils, 1070 aluminum coils, and 1100 aluminum coils, the process is relatively single, and the technology is quite mature. So, the price is cheaper. It also means that the highly economical 1000 series pure aluminum is currently one of the most commonly used series in conventional industry and is ideal for large-scale applications in industrial manufacturing. If you need more specific information about 1050 aluminum rolls, don’t hesitate to contact our sales team!
Physical Characteristics of 1060 Aluminum Alloy
Physical Property | Value |
---|---|
Density | 2.71g/cm3 |
Hardness Brinell | 20-30HB |
Melting Point | 650°C |
Thermal Expansion | 24 x10^-6 /°C |
Thermal Conductivity | 237W/m.K |
Electrical Resistivity | 0.0282 x10^-6 Ω.m |
Mechanical Property | Value |
---|---|
Tensile Strength | 60 – 125 MPa |
Compressive Strength | ≥115MPa |
Yield Strength | 20-115 MPa |
Elasticity Modulus | ≥70Gpa |
Elongation | ≥20% |
Elongation at Break | ≥2.3% |
1060 aluminum coil Corrosion resistance
1060 aluminum coil chemical properties are very active. At 20℃, its standard potential is -1.69V, which makes it easy to form a firm and tight oxide film by the action of oxygen in the air, and the standard point is raised to -0.5V. So, aluminum is resistant to corrosion in the atmosphere. However, with the increase of impurities, the continuity of the oxide film is destroyed to form a micro battery, reducing its corrosion resistance.
The corrosion resistance of the 1060 aluminum coil in pure water mainly depends on the water temperature, water quality, and aluminum purity. When the water temperature is lower than 50℃, with the improvement of water quality and aluminum purity, the corrosion resistance of the 1060 aluminum coil is improved, and the corrosion appearance is mainly spot-like. If the water contains a small quantity of active ions (Cl-, Cu+, etc.), the corrosion resistance of aluminum is sharply reduced.
The corrosion resistance of 1060 aluminum coil in acid and alkali is roughly as follows
Medium | Anti-corrosion Capability |
---|---|
Ocean Water | weak |
Salt | weak |
Organic Acid | Common |
fluorine, chlorine, bromine, Lodine | Poor |
hydrochloric acid, hydrofluoric acid, acetic acid | Poor |
alkaline, ammonia water, Lime water | Poor |
dilute sulfuric acid, dilute nitric acid | Poor |
ammonia Gas, sulfurous gas | Good |
Cold concentrated sulfuric acid, Cold concentrated nitric acid | Stable |
petroleum, kerosene, ethyl alcohol, benzene, organic compound, etc | Stable |
1060 aluminum coil annealing process
1060 aluminum coil Features
- A high degree of purity: The 1060 aluminum coil is industrial pure aluminum, and its aluminum content exceeds 99.60%. So, the texture is relatively soft.
- Lightweight: 1060 aluminum alloy has a low density of about 2.7g/cm³, which is 1/3 of steel, so it has significant application value in many fields.
- Machinability: Because 1060 aluminum alloy has a soft texture, good plasticity, and machinability, the 1060 aluminum coil can be manufactured by die casting, extrusion, forging, and other processes. But, in the machinery process, it is easy to produce bending, deformation, and other problems. Therefore, it is necessary to anneal before processing to improve its plasticity and processing properties.
- Good conductivity: Aluminum has good electrical conductivity, and 1060 aluminum alloy is widely used as a conductive material in wires and cables.
- Good thermal conductivity: 1060 aluminum alloy has good thermal conductivity and is suitable for manufacturing equipment with high heat conduction requirements such as radiators and heat exchangers.
- Corrosion resistance: 1060 aluminum alloy has good corrosion resistance, especially in the atmosphere and many chemical media.
1060 aluminum coil annealing process
The annealing process of the 1060 aluminum coil generally includes two steps: preheating and annealing. Preheating is to homogenize the temperature inside the aluminum coil to prevent deformation during the annealing process. Annealing is to improve the plasticity and processing properties of aluminum coils. In the annealing process, it is necessary to control the temperature and time to ensure the annealing effect. The specific process flow is as follows:
Aluminum Coil preheating
To ensure temperature homogenization, the 1060 aluminum coils must be heated to an appropriate temperature during the preheating phase. Under normal circumstances, the preheating temperature is about 200℃, and the preheating time is 30 minutes.
Aluminum coil annealing
In the annealing phase, the 1060 aluminum coils must be heated to another appropriate temperature to improve their plasticity and processability. Generally speaking, the annealing temperature is about 370℃, and the annealing time is 2-3 hours. The aluminum coil needs to be placed in the annealing furnace to control the furnace temperature and the position of the coil material to ensure uniform temperature.
Aluminum coil cooling
After the annealing, the aluminum coil must be removed and placed in a ventilated place for natural cooling. The cooling time needs to be determined according to the thickness and size of the 1060 aluminum coil. Please note that during the cooling process, care should be taken to prevent the surface of the aluminum coil from being damaged.
Aluminum coil surface treatment
After the aluminum coil is cooled, its surface must be treated to ensure its surface finish and product quality. Specific treatment methods include grinding, polishing, and so on.
Aluminum coil quality testing
After the annealing and cooling of the aluminum coil, it is also necessary to conduct a quality detection to ensure that its quality meets the requirements. The content of quality inspection includes appearance, size, mechanical properties, and so on.
Aluminum coil packaging
After the process above is completed, the aluminum coils need packaging to ensure they are not damaged during transportation. Packaging materials must choose good quality, moisture-proof, and shock-proof materials to ensure the integrity of the aluminum coil.
In summary, the annealing process of the 1060 aluminum coil includes preheating, annealing, cooling, surface treatment, quality inspection, packaging, and other links. The parameters and requirements of each link must be controlled to ensure the annealing effect and product quality.
The Application of 1060 Prepainted Aluminum Coil
In materials science, 1060 aluminum coil is a high-purity aluminum product with an aluminum content of up to 99.60% or more. It is recognized as an industrial-grade pure aluminum material. This aluminum quality light plasticity is easy to form and can be welded. With excellent processing performance, corrosion resistance, and good electrical and thermal conductivity, it is ideal for metal processing materials. Moreover, the 1060 aluminum coil, with its flat shape, precise geometric size, and high surface gloss, is a visually appealing choice. Its competitive pricing, relative to other series of aluminum coils, ensures a wide range of application prospects.
Architectural Decoration Field
The 1060 aluminum coil, with its exceptional corrosion resistance and aesthetic appeal, has revolutionized architectural decoration. Whether it’s used for curtain walls, roofs, ceilings, window frames, or other materials, its lightweight and high-strength properties enhance the beauty of buildings and improve their safety and durability, giving them a modern architectural touch. Moreover, the 1060 aluminum coil’s outstanding thermal insulation performance contributes to the energy efficiency of buildings, making it a truly innovative building material.
Electronics and Electrical Appliances
The 1060 aluminum coil is favored in electronics and electrical appliances for its conductivity and good heat dissipation performance. Its high electrical conductivity and good processability make electronic and electrical products more efficient and stable. This also makes it an ideal material for manufacturing electronic components, wires, cables, heat sinks, and other product components, such as specific electronic and electrical products.
Furthermore, the 1060 aluminum coil is a high-quality sealing material, protecting electrical equipment such as cables, capacitor housings, and battery casings from moisture, oxidation, and corrosion. This not only ensures the safety of the equipment but also extends its service life, providing a sense of reassurance to electrical professionals.
transportation industry
In transportation, the 1060 aluminum coil also plays an indispensable role. Taking the well-known car manufacturer BYD as an example, the company has used a large amount of 1060 aluminum coils as the material for the body and components of new energy vehicles. Through practical applications, it has been proven that the 1060 aluminum coil can not only effectively reduce the weight of the vehicle body but increase the vehicle’s range (according to BYD’s data report, after using the 1060 aluminum coil, the vehicle weight is reduced by 30% and the range is increased by 20%), and its excellent corrosion resistance dramatically extends the service life of the vehicle. Moreover, the company also uses the 1060 aluminum coil to produce parts such as car heat shields and radiators, further improving the vehicle’s performance and comfort. Using 1060 aluminum coils in new energy vehicles contributes to environmental sustainability through specific environmental benefits.
In addition, the 1060 aluminum coil is also used to manufacture the shells and bodies of transportation vehicles such as aircraft, high-speed trains, and ships. Its lightweight characteristics also help reduce transportation vehicles’ self-weight, improving transportation efficiency. At the same time, its high strength and corrosion resistance also enable transportation vehicles to perform well in harsh environments.
packaging industry
In the packaging industry, the 1060 aluminum coil has become an ideal choice for manufacturing various packaging materials due to its excellent corrosion resistance and good processability. Especially in the packaging of food, medicines, cosmetics, etc., the 1060 aluminum coil, with its excellent insulation, moisture resistance, and oxidation resistance, has become an indispensable material. The 1060 aluminum coil is commonly used to produce food aluminum foil bags, cans, aluminum boxes, aluminum foil packaging paper, and other products. These packaging materials are beautiful and ensure that the products are effectively protected from light, oxygen, odors, and moisture during storage and transportation, extending the shelf life of the products.
In addition, the 1060 aluminum coil is also widely used in the baking industry. During the baking process, the baking paper and baking trays made of the 1060 aluminum coil are favored for their excellent thermal conductivity and high-temperature resistance. They can help bake food evenly and maintain the texture and color. According to market research agencies, the global aluminum foil packaging market is expanding. It is expected to grow at an average annual rate of 5% in the coming years.
medical device industry
The 1060 aluminum coil is widely used to produce medical devices, dressings, and other products. These 1060 aluminum products, with good antibacterial properties and non-toxic and harmless characteristics, can provide patients with safer and more reliable medical care. According to statistics, using medical devices made from the 1060 aluminum coil has reduced the infection rate by 25%. In addition, its lightweight characteristics make medical devices more accessible to carry and operate.
To sum up, the 1060 aluminum coil occupies a pivotal position as a multifunctional material, with its unique performance and wide range of application fields.
According to market research data, 1060 aluminum coils in various fields of application are showing a steady rise. Taking the packaging industry as an example, according to statistics, the global aluminum foil packaging market is expected to grow at an average annual rate of 5% in the next few years. This growth is mainly due to consumer demand for food safety and preservation and the favor of environmentally friendly packaging materials.
In the future, with technology constantly innovating and market demand escalating, the 1060 aluminum market application volume will also expand and deepen. For example, to meet the needs of the packaging industry, the production process and alloying element ratio of the 1060 aluminum coil are being optimized to improve its electrical conductivity, thermal conductivity, strength, and other properties. This adaptability of the 1060 aluminum coil to different industries is a key factor in its growing demand.
At the same time, with the rapid development of high-tech industries such as new energy vehicles and aerospace, the application of 1060 aluminum coil in these fields will also usher in a broader market space.
WanTai Aluminum Industry Product List
Aluminum Alloy Series | Aluminum Grade |
---|---|
1000 Series | 1050, 1060, 1070, 1100, etc. |
2000 Series | 2014, 2017, 2024, 2A11, 2A12, 2A14, etc. |
3000 Series | 3003, 3004, 3005, 3104, 3105, 3A12, etc. |
4000 Series | 4004, 4032, 4043, 4047, 4A03, 4A11, 4A13, 4A17, etc. |
5000 Series | 5005, 5052, 5052A, 5052B, 5059, 5083, 5086, 5182, 5252, 5454, 5754, 5A02, 5A03, 5A05, 5A06, 5M49, 5M52, etc. |
6000 Series | 6005, 6005A, 6060, 6061, 6063, 6082, 6101, etc. |
7000 Series | 7005, 7050, 7075, 7A04, 7A09, etc. |
8000 Series | 8011, 8076, 8077, 8079, 8176, 8177, 8276, 8280, etc. |
Types | Aluminum Coil, Aluminum sheet, Aluminum foil, Aluminum strip, Checkered Plate or diamond plate, etc. |
Length(mm) | customizable as required. |
Width(mm) | 40mm-2650mm |
Thickness(mm) | 0.006mm-800mm |
surface | oxidation, Precoating, wire drawing, Mirror Finishing, embossing, etc. |
payment | T/T, L/C, D/P, etc. |
package | Wrap in plastic or kraft paper with Moisture-proof desiccant. Pack in fumigated wooden cases and brackets. |
Different Specifications of Aluminum Coil Parameters
The following are examples of different specifications of aluminum rolls and their weight and length information for Reference:
specification | Thickness(M) | Area(m2) | Weight(Kg) |
---|---|---|---|
0.5mmx1mx1000m | 0.0005 | 1000 | 1,350 |
0.6mmx1mx1000m | 0.0006 | 1000 | 1,620 |
0.8mmx1mx1000m | 0.0008 | 1000 | 2,160 |
1.0mmx1mx1000m | 0.0010 | 1000 | 2,700 |
1.5mmx1mx1000m | 0.0015 | 1000 | 4,050 |
2.0mmx1mx1000m | 0.0020 | 1000 | 5,400 |
2.5mmx1mx1000m | 0.0025 | 1000 | 6,750 |
3.0mmx1mx1000m | 0.0030 | 1000 | 8,100 |
Interested In Working With WANTAI?
Please insert your contact information into the following contact form and let us know how we can help you! We will contact you as quickly as possible.
People Also Searched for 1060 Aluminum Coil
Aluminum Coil Uses, Aluminum Coil Exporter In China, Aluminum Coil Price In India, Aluminum Coil, Aluminum Coil Price Per Kg, Aluminum Coil Hs Code, Aluminum Coil Supplier In Delhi, 1050 Aluminum Coils Suppliers, CC Casting Aluminum Coil, Al 1050 Coil, Aluminum Alloy 1050 Coils Stockholders, Aluminum 1050 Coils Exporters, Aluminum 1050 Coils Manufacturers, Aluminum Alloy 1050 Coil Size, Aluminum Alloy 1050 Slitting Coil, Aluminum Alloy 1050 Coils Price List India, 1050 Aluminum Coils, Al Alloy 1050 Coil, Aluminum 1050 Coils, 1050 Aluminum Coil Distributors, Aluminum Alloy 1050 Coils, Aluminum Coils Suppliers, Aluminum Alloy 1050 Coil Supplier, Aluminum UNS A91050 Slit Coils Exporters, Aluminum 1050 Slitting Coil Manufacturers, Aluminum Alloy 1050 Coil Price, Aluminum Alloy 1050 Coils Distributors, Aluminum Alloy 1050 Coil, Aluminum Alloy 1050 Coils Stock, Aluminum 1050 Coil Exporter, 1050 Aluminum Coil price, 1050 Aluminum Coil size, 1050 Aluminum Coil for sale, Aluminum 1050 chemical composition, 1050 H14 Aluminum, etc.