1100 Aluminum Coil
1100 Aluminum Coil
Application Market: CTP/PS plate base, aluminum-plastic plate, lamp material, capacitor shell, battery explosion-proof valve, building exterior wall, road sign, tab material, etc.
Width: 40-2650mm | ||
Thickness: 0.2-5mm | ||
Length: Customizable | ||
Mother Coil: DC or CC | ||
Temper: O, H14, H18, H22, H24, etc. | ||
Surface: Mill Finishing, Mirror Finishing, Checkered | ||
Free Sample Size: A4 Paper Size | ||
MOQ: 3T | ||
Payment Terms: T/T, L/C, D/P | ||
Delivery Time: Normally Within 15-30Days |
An aluminum coil is a rolled metal product calendered by a finishing mill and processed by drawing and bending angles without smooth flying shear. It is the raw material of aluminum strips and plates. The slitting equipment can cut the aluminum roll into strips, and the flattening equipment can make the aluminum roll into a sheet.
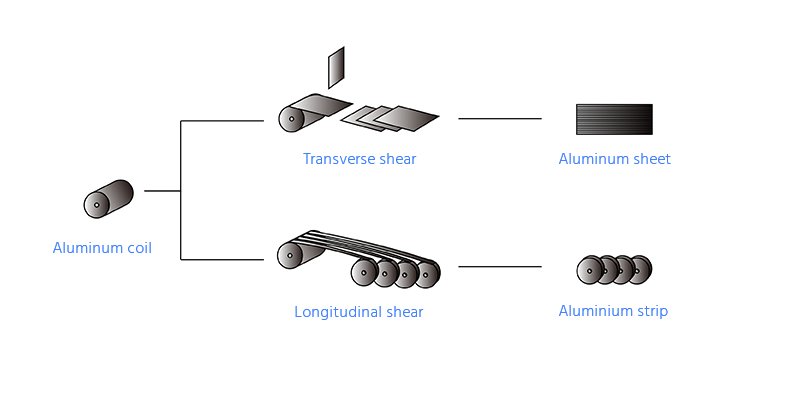
1100 Aluminum Coil DC / CC International Alloy designation (For Reference)
The normal 1100 aluminum coil and pre-painted 1100 aluminum coil parameters are identical to the International Alloy Designations System for 1100 Aluminum sheets.
Alloy Series | National Standard | American Standard | Europe Standard |
---|---|---|---|
1000 Series | 1100 Aluminum Coil | 1100 Aluminum Coil | – |
Components of 1100 Aluminum Coil
Chemical composition | Content(%) |
---|---|
Si+Fe | ≤0.95 |
Cu | 0.05-0.20 |
Zn | ≤0.10 |
Mn | ≤0.05 |
Al | ≥99.00 |
1100 aluminum coil belongs to 1 series aluminum alloy. Like 1050 aluminum sheet/coil and 1060 aluminum sheet/coil, 1100 aluminum coil is industrial pure aluminum. The aluminum content of the 1100 aluminum coil is greater than 99%, and the texture is relatively soft, but it has excellent ductility, formability, and good plasticity.
At the same time, the 1100 aluminum coil also has the advantages of low density, high tensile strength, high corrosion resistance, good electrical and thermal conductivity, and high weldability. After anodizing, the corrosion resistance can be further improved, while a more beautiful surface can be obtained. However, 1100 series aluminum cannot be strengthened by heat treatment.
1100 Aluminum Coil DC / CC Temper designation (For Reference)
Temper | Definition |
---|---|
O | Annealed |
H12 | Strain Hardened, 1/4 Hard |
H14 | Strain Hardened, 1/2 Hard |
H16 | Strain Hardened, 3/4 Hard |
H18 | Strain Hardened, Full Hard |
H22 | Strain Hardened and Partially Annealed, 1/4 Hard |
H24 | Strain Hardened and Partially Annealed, 1/2 Hard |
H26 | Strain Hardened and Partially Annealed, 3/4 Hard |
H28 | Strain Hardened and Partially Annealed, Full Hard |
Aluminum, known for its small density, good plasticity, and excellent formability, is a material of choice for applications that require high corrosion resistance and low strength. These applications include sheet metal products, hollow metal, radiators, welding key combinations, reflectors, nameplates, and more. WanTai specializes in the manufacturing of aluminum coils, including prepainted aluminum coils. Our products are designed to cater to the specific needs of industries such as automotive, transformers, air compressors, construction machinery, and air separation equipment. They are used to manufacture various parts, including radiators, condensers, and evaporators.
Advanced Color-Coated Process
Polyester-coated pre-coating Technology(PE Coating)
The polyester coating is a kind of anti-UV UV polyester resin coating; its main component uses polymers containing ester bonds in the main chain as monomers, adding alkyd resin and an ultraviolet absorber. After baking polyester coating on the surface of aluminum (aluminum sheet, aluminum roll) many times, it forms a solid film with protection and decoration. The polyester coating protects color-coated aluminum products (aluminum sheets, aluminum rolls) from exposure to the atmosphere due to temperature differences, freeze-thaw cycles, corrosive gases and microorganisms, ultraviolet radiation, wind, rain, frost, and snow.
In addition, the polyester coating can give color-coated aluminum substrate products rich color. According to gloss, the polyester coating can be divided into matte and highlight series. Therefore, the color-coated aluminum coil not only has good gloss and smoothness but also superior texture and feel and can also increase the sense of layer and three-dimensionality. It is especially suitable for interior decoration and advertising boards.
polyvinylidene difluoride coating technology(PVDF Coating)
Fluorocarbon coating is PVDF resin. It mainly refers to vinylidene fluoride homopolymer or vinylidene fluoride and other small amounts of fluorinated vinyl monomer copolymer coatings. The fluoric acid-base material with a fluorine/carbonization bond has a stable and firm chemical structure, which makes the physical properties of fluorocarbon coatings different from those of general coatings.
Fluorocarbon coatings can be divided into traditional fluorocarbon coatings and nano-fluorocarbon coatings according to the film formation structure of the surface. In 1965, the Pennwalt Chemical Company of the United States, for the first time, used fluorocarbon paint for the coating of indoor and outdoor aluminum in high-grade buildings, a wide range of color selectivity, solemn appearance, and durability for many magnificent curtain wall buildings around the world added luster. In addition to the wear and impact resistance in terms of mechanical properties, it also shows excellent and long-term fading resistance and UV resistance in harsh climates and humid environments. After high-temperature grilling, the molecular structure of the coating is tight, and the machine has superior weather resistance. The coating manufacturer’s guarantee of the service life of the coating began to be 10 years, 15 years to guarantee more than 20 years.
American research institutions have tested and compared fluorocarbon, super, and general coatings. The samples of the coatings were exposed to hot sunlight in Florida, the United States, and exposed to the harsh environment of humid salty air for 12 years, which proves that the stability and durability of fluorocarbon coatings are 30%-80% higher than those of the other two coatings. Fluorocarbon coatings ensure that they can be used in various harsh environments. It is especially suitable for indoor and outdoor decoration in public places, commercial chains, exhibition advertising, and other decorations and displays.
1100 Corrosion resistance
1100 aluminum coil chemical properties are very active. At 20℃, its standard potential is -1.69V, which makes it easy to form a firm and tight oxide film by the action of oxygen in the air, and the standard point is raised to -0.5V. So, aluminum is resistant to corrosion in the atmosphere. However, with the increase of impurities, the continuity of the oxide film is destroyed to form a micro battery, reducing its corrosion resistance.
The corrosion resistance of the 1100 aluminum coil in pure water mainly depends on the water temperature, water quality, and aluminum purity. When the water temperature is lower than 50℃, with the improvement of water quality and aluminum purity, the corrosion resistance of the 1100 aluminum coil is improved, and the corrosion appearance is mainly spot-like. If the water contains a small quantity of active ions (Cl-, Cu+, etc.), the corrosion resistance of aluminum is sharply reduced.
The corrosion resistance of 1100 aluminum coil in acid and alkali is roughly as follows
Medium | Anti-corrosion Capability |
---|---|
Ocean Water | weak |
Salt | weak |
Organic Acid | Common |
fluorine, chlorine, bromine, Lodine | Poor |
hydrochloric acid, hydrofluoric acid, acetic acid | Poor |
alkaline, ammonia water, Lime water | Poor |
dilute sulfuric acid, dilute nitric acid | Poor |
ammonia Gas, sulfurous gas | Good |
Cold concentrated sulfuric acid, Cold concentrated nitric acid | Stable |
petroleum, kerosene, ethyl alcohol, benzene, organic compound, etc | Stable |
1100 aluminum coil annealing process
1100 aluminum coil Features
- A high degree of purity: The 1100 aluminum coil is industrial pure aluminum, and its aluminum content exceeds 99%. So, the texture is relatively soft.
- Lightweight: 1100 aluminum alloy has a low density of about 2.7g/cm³, which is 1/3 of steel, so it has important application value in many fields.
- Machinability: Because 1100 aluminum alloy has a soft texture, good plasticity, and machinability, the 1100 aluminum coil can be manufactured by die casting, extrusion, forging, and other processes. But, in the machinery process, it is easy to produce bending, deformation, and other problems. Therefore, it is necessary to anneal before processing to improve its plasticity and processing properties.
- Good conductivity: Aluminum has good electrical conductivity, and 1100 aluminum alloy is widely used as a conductive material in wires and cables.
- Good thermal conductivity: 1100 aluminum alloy has good thermal conductivity and is suitable for manufacturing equipment with high heat conduction requirements such as radiators and heat exchangers.
- Corrosion resistance: 1100 aluminum alloy has good corrosion resistance, especially in the atmosphere and many chemical media.
1100 aluminum coil annealing process
The annealing process of the 1100 aluminum coil generally includes two steps: preheating and annealing. Preheating is to homogenize the temperature inside the aluminum coil to prevent deformation during the annealing process. Annealing is to improve the plasticity and processing properties of aluminum coils. In the annealing process, it is necessary to control the temperature and time to ensure the annealing effect. The specific process flow is as follows:
Aluminum Coil preheating
During the preheating phase, the aluminum coils need heating to an appropriate temperature to ensure the temperature homogenization inside. Under normal circumstances, the preheating temperature is about 200℃, and the preheating time is 30 minutes. In the preheating process, it is necessary to pay attention to the placement of the aluminum coil to ensure uniform temperature.
Aluminium coil annealing
In the annealing phase, the aluminum coils must be heated to another appropriate temperature to improve their plasticity and processability. Generally speaking, the annealing temperature is about 370℃, and the annealing time is 2-3 hours. The aluminum coil needs to be placed in the annealing furnace to control the furnace temperature and the position of the coil material to ensure uniform temperature.
Aluminum coil cooling
After the annealing is completed, the aluminum coil needs to be removed and placed in a ventilated place for natural cooling. The cooling time needs to be determined according to the thickness and size of the aluminum coil. Attention please, during the cooling process, care should be taken to prevent the surface of the aluminum coil from being damaged.
Aluminum coil surface treatment
After the aluminum coil is cooled, its surface must be treated to ensure its surface finish and product quality. Specific treatment methods include grinding, polishing, and so on.
Aluminum coil quality testing
After the annealing and cooling of the aluminum coil, it is also necessary to conduct a quality detection to ensure that its quality meets the requirements. The content of quality inspection includes appearance, size, mechanical properties, and so on.
Aluminum coil packaging
After the process above is completed, the aluminum coils need packaging to ensure they are not damaged during transportation. Packaging materials must choose good quality, moisture-proof, and shock-proof materials to ensure the integrity of the aluminum coil.
In summary, the annealing process of the 1100 aluminum coil includes preheating, annealing, cooling, surface treatment, quality inspection, packaging, and other links. The parameters and requirements of each link must be controlled to ensure the annealing effect and product quality.
The Application of 1100 Aluminum Coil(Prepainted Aluminum Coil)
In materials science, the 1100 aluminum coil, with its excellent corrosion resistance, formability, and riched color-coating, has become indispensable for many industries. The following content combines scientific data and practical cases to discuss the application and excellent performance of 1100 aluminum coils in various fields.
building construction
The 1100 aluminum coil is favored in the construction industry for its excellent corrosion resistance, plasticity, and lightweight characteristics. In addition, due to its coating properties, 1100 aluminum coils (pre-coated aluminum coils) are often used to make components such as building exterior panels, roof panels, and ceilings. The surface of the 1100 aluminum coil is smooth and flat. It provides a beautiful appearance, has good fire performance, and can effectively prevent the spread of fire. According to statistics, the annual demand for 1100 aluminum coils in the global construction field has reached hundreds of thousands of tons. With the continuous development of the construction industry, this demand is still rising yearly.
Packaging field
1100 aluminum rolls are widely used in packaging because of their good corrosion resistance and sealing properties. It is often used in packaging products such as food, medicine, and cosmetics. Through coating treatment, the surface of the 1100 aluminum coil can further improve the corrosion resistance and oxidation resistance, ensuring the quality and safety of the packaged goods. In addition, the exquisite appearance and recyclability of the color-coated 1100 aluminum coil also make it an ideal choice for environmentally friendly packaging materials. According to market research data, the demand for 1100 aluminum coils in the packaging industry has increased by 17% yearly, becoming one of its important application areas.
Electronic Field
The 1100 aluminum coil has attracted much attention in electronics due to its excellent electrical and thermal conductivity. It is often used to manufacture key components such as electronic radiators, packaging materials, and circuit boards. In the manufacture of electronic products, 1100 aluminum coils can effectively dissipate heat, maintain the working stability of electronic components, and have good electromagnetic shielding performance to reduce electromagnetic interference. With the popularization of electronic products and the acceleration of replacement, the demand for 1100 aluminum coils in the electronics field will continue to grow.
automobile making
The 1100 aluminum coil also shows its unique advantages in the automobile manufacturing industry. Due to its low density and good plasticity, it is widely used to manufacture automobile bodies and body parts. Lightweight is one of the important trends in automotive manufacturing, and the lightweight characteristics of the 1100 aluminum coil can significantly reduce the vehicle’s overall weight and improve fuel efficiency. At the same time, its high strength can also provide good safety performance. According to data released by the International Aluminum Association, the annual demand for 1100 aluminum rolls in the global automobile manufacturing industry has reached hundreds of thousands of tons and is still growing steadily.
aerospace field
The 1100 aluminum coil is widely used in aerospace because of its good mechanical properties and corrosion resistance. In aircraft manufacturing, the aluminum plate makes important parts such as the fuselage, wings, and skin. Its lightweight and high-strength characteristics can meet the high requirements for material properties in aerospace while reducing the aircraft’s overall weight and improving fuel efficiency. With the continuous development of aerospace technology, 1100 aluminum coils will have a broader application prospect in this field.
Sports equipment
1100 aluminum rolls also play an important role in sports equipment. Because of its lightweight, high strength, corrosion resistance, and other advantages, it is often used to manufacture sports equipment. For example, bicycle frames, golf clubs, skis, and other sports equipment can be seen in the figure of 1100 aluminum rolls. These devices are not only beautiful but also have excellent performance, which can meet the high requirements of athletes for equipment.
Heat exchanger field
The application of 1100 aluminum coils in heat exchangers is also increasing. A heat exchanger is a kind of equipment widely used in chemical, petroleum, electric power, and other fields to achieve heat transfer and exchange. Because of its good thermal conductivity and corrosion resistance, the 1100 aluminum coil is often used to manufacture fins, pipes, and other components of heat exchangers. These components can withstand high temperature and pressure environments to ensure the normal operation of the heat exchanger.
Printing industry
The 1100 aluminum coil also has a wide range of applications in the printing industry. Because of its smooth surface, easy printing, and good corrosion resistance, it is often used as a printing substrate. 1100 aluminum rolls provide stable print quality and long service life, whether offset, intaglio, or flexo printing. At the same time, its recyclability also aligns with the trend of environmentally friendly printing.
Mold manufacturing
In mold manufacturing, 1100 aluminum coils are favored for their good plasticity and processability. They are often used to manufacture mold substrates or parts, such as injection molds and die-casting molds. Because the 1100 aluminum coil is easy to process into various shapes, it can meet the complex requirements of mold manufacturing, while its excellent mechanical properties can also ensure the mold’s stability and durability.
shipbuilding
In shipbuilding, the application of 1100 aluminum coils is also gradually increasing. Its lightweight, high-strength, and corrosion-resistant properties make it an ideal material for manufacturing ship structural parts and decorative parts. Whether it is a luxury yacht or a large cargo ship, you can see the figure of 1100 aluminum coils. Its application not only reduces the overall weight of the ship by 30% and improves the sailing performance, but also enhances the corrosion resistance and extends the ship’s service life by 20%.
solar energy industry
In the solar industry, 1100 aluminum coils are widely used to manufacture solar mirrors and panels. Their good thermal conductivity and corrosion resistance make them important materials for solar energy equipment. By reflecting sunlight or acting as a support structure for solar panels, 1100 aluminum coils play an important role in the operation and efficiency of solar equipment.
medical device
1100 aluminum coils are used in medical equipment because of their good biocompatibility and corrosion resistance. They are often used to manufacture medical device enclosures, brackets, and other components. These components must have good mechanical properties and corrosion resistance to ensure the normal operation of medical devices and the safety of patients.
Lighting and reflective equipment
In lighting and reflective equipment, 1100 aluminum coils are often used to make reflective panels and luminaire housings. Due to its excellent reflective performance and corrosion resistance, it can ensure efficient lighting and long-term stable operation of the lamp.
chemical industry
In the chemical industry, 1100 aluminum coils are often used to manufacture containers and pipes. Their corrosion resistance and sealing performance effectively prevent the leakage and pollution of chemical substances and ensure production safety.
utility industry
In the power industry, 1100 aluminum coils are often used to manufacture power transmission and distribution equipment. Due to their lightweight, high strength, and excellent electrical conductivity, they can reduce the equipment’s overall weight and power loss and improve its efficiency.
Decoration Industry
1100 aluminum rolls are often used in the decoration industry to manufacture decorative materials such as panels, screens, and partitions. Its surface can be a variety of surface treatments, such as spraying, oxidation, coloring, etc., to meet the needs of different decorative styles.
Transportation
1100 aluminum coils are also widely used in transportation. For example, they are often used to manufacture interior panels, luggage racks, and other components in rail transit vehicles. In the aerospace sector, they can also be used to manufacture aircraft skins, propellers, and other parts accessories.
Having said all of the above, with its unique physical and chemical properties, the 1100 aluminum coil has shown a wide range of application prospects in many fields. No matter what construction, packaging, electronics, automotive manufacturing, aerospace, sports equipment heat exchangers, and other fields, 1100 aluminum rolls play an irreplaceable role. In short, with the deepening of material science research, the improvement of processing technology, and the continuous development of the market, the application field of 1100 aluminum coils will continue to expand. Especially in the new energy vehicles, renewable energy, and environmental protection field, 1100 aluminum rolls will play a more important role.
Different Specifications of Aluminum Coil Parameters
The following are examples of different specifications of aluminum rolls and their weight and length information for reference:
specification | Thickness(M) | Area(m2) | Weight(Kg) |
---|---|---|---|
0.5mmx1mx1000m | 0.0005 | 1000 | 1,350 |
0.6mmx1mx1000m | 0.0006 | 1000 | 1,620 |
0.8mmx1mx1000m | 0.0008 | 1000 | 2,160 |
1.0mmx1mx1000m | 0.0010 | 1000 | 2,700 |
1.5mmx1mx1000m | 0.0015 | 1000 | 4,050 |
2.0mmx1mx1000m | 0.0020 | 1000 | 5,400 |
2.5mmx1mx1000m | 0.0025 | 1000 | 6,750 |
3.0mmx1mx1000m | 0.0030 | 1000 | 8,100 |
Interested In Working With WANTAI?
Please insert your contact information into the following contact form and let us know how we can help you! We will contact you as quickly as possible.