Color Coated Aluminum metal
Best painted Aluminum metal Factory You Could Find In China
Color-coated aluminum (aluminum sheet, aluminum coil), is a new type of environmentally friendly metal decorative aluminum. Its unique color, durability, excellent corrosion and rust resistance, wear resistance, and excellent adhesion and flexibility make it widely used in many fields such as construction, industrial production, and electronic products. At the same time, because of its good color stability, outdoor durability, and weather resistance, color-coated aluminum coil in the decoration, transportation, packaging, and other fields also shows a huge market potential.
Color-coated aluminum coil/sheet, as the name suggests, is a specific aluminum coil/sheet for painting and coloring the surface of the aluminum substrate. The production process includes the pre-treatment of aluminum plates, surface coating, and post-treatment steps, each step strictly follows the principles of material science to ensure the quality and performance of products. There are many kinds of surface coatings on color-coated aluminum coils, and the common coating processes are polyester-coated aluminum coils (PE) and fluorocarbon-coated aluminum coils (PVDF). Fluorocarbon coatings are known for their excellent corrosion resistance, anti-aging properties, and high adhesion. The polyester coating is characterized by bright color and good color retention. These coatings not only enhance the decoration of aluminum but also improve its service life and weather resistance.
5052 Aluminum Sheet
3105 Aluminum Sheet
1100 Aluminum Sheet
3003 Aluminum Sheet
3004 Aluminum Sheet
Advanced Color-Coated Process
Polyester-coated pre-coating Technology(PE)
The polyester coating is a kind of anti-UV UV polyester resin coating; its primary component uses polymers containing ester bonds in the main chain as a monomer, adding alkyd resin and an ultraviolet absorber. After baking polyester coating on the surface of aluminum (aluminum sheet, aluminum roll) many times, it forms a solid film with protection and decoration. The polyester coating protects color-coated aluminum products (aluminum sheets, aluminum rolls) from exposure to the atmosphere due to temperature differences, freeze-thaw cycles, corrosive gases and microorganisms, ultraviolet radiation, wind, rain, frost, and snow.
In addition, the polyester coating can give color-coated aluminum substrate products rich color. According to gloss, the polyester coating can be divided into matte and highlight series. Therefore, the color-coated aluminum coil not only has good gloss and smoothness but also superior texture and feel and can also increase the sense of layer and three-dimensionality. It is especially suitable for interior decoration and advertising boards.
polyvinylidene difluoride coating technology(PVDF)
Fluorocarbon coating is PVDF resin. It mainly refers to vinylidene fluoride homopolymer or vinylidene fluoride and other small amounts of fluorinated vinyl monomer copolymer coatings. The fluoric acid-base material with a fluorine/carbonization bond has a stable and firm chemical structure, which makes the physical properties of fluorocarbon coatings different from those of general coatings.
Fluorocarbon coatings can be divided into traditional fluorocarbon coatings and nano-fluorocarbon coatings according to the film formation structure of the surface. In 1965, the Pennwalt Chemical Company of the United States, for the first time, used fluorocarbon paint for the coating of indoor and outdoor aluminum in high-grade buildings, a wide range of color selectivity, solemn appearance, and durability for many magnificent curtain wall buildings around the world added luster. In addition to the wear and impact resistance in terms of mechanical properties, it also shows excellent and long-term fading resistance and UV resistance in harsh climates and humid environments. After high-temperature grilling, the molecular structure of the coating is tight, and the machine has superior weather resistance. The coating manufacturer’s guarantee of the service life of the coating began to be ten years, 15 years to guarantee more than 20 years.
American research institutions have tested and compared fluorocarbon, super, and general coatings. The samples of the coatings were exposed to hot sunlight in Florida, the United States, and exposed to the harsh environment of humid salty air for 12 years, which proves that the stability and durability of fluorocarbon coatings are 30%-80% higher than those of the other two coatings. Fluorocarbon coatings ensure that they can be used in various harsh environments. It is especially suitable for indoor and outdoor decoration in public places, commercial chains, exhibition advertising, and other decorations and displays.
1100 Aluminum Coil
1050 Aluminum Coil
1060 Aluminum Coil
3003 Aluminum Coil
3004 Aluminum Coil
3104 Aluminum Coil
3105 Aluminum Coil
Advanced Color-Coated Process
Polyester-coated pre-coating Technology(PE)
The polyester coating is a kind of anti-UV UV polyester resin coating; its central component uses polymers containing ester bonds in the main chain as a monomer, adding alkyd resin and an ultraviolet absorber. After baking polyester coating on the surface of aluminum (aluminum sheet, aluminum coil) many times, it forms a solid film with protection and decoration. The polyester coating protects color-coated aluminum products (aluminum sheets, aluminum rolls) from exposure to the atmosphere due to temperature differences, freeze-thaw cycles, corrosive gases and microorganisms, ultraviolet radiation, wind, rain, frost, and snow.
In addition, the polyester coating can give color-coated aluminum substrate products rich color. According to gloss, the polyester coating can be divided into matte and highlight series. Therefore, the color-coated aluminum coil not only has good gloss and smoothness but also superior texture and feel and can also increase the sense of layer and three-dimensionality. It is especially suitable for interior decoration and advertising boards.
polyvinylidene difluoride coating technology(PVDF)
Fluorocarbon coating is PVDF resin. It mainly refers to vinylidene fluoride homopolymer or vinylidene fluoride and other small amounts of fluorinated vinyl monomer copolymer coatings. The fluoric acid-base material with a fluorine/carbonization bond has a stable and firm chemical structure, which makes the physical properties of fluorocarbon coatings different from those of general coatings.
Fluorocarbon coatings can be divided into traditional fluorocarbon coatings and nano-fluorocarbon coatings according to the film formation structure of the surface. In 1965, the Pennwalt Chemical Company of the United States, for the first time, used fluorocarbon paint for the coating of indoor and outdoor aluminum in high-grade buildings, a wide range of color selectivity, solemn appearance, and durability for many magnificent curtain wall buildings around the world added luster. In addition to the wear and impact resistance in terms of mechanical properties, it also shows excellent and long-term fading resistance and UV resistance in harsh climates and humid environments. After high-temperature grilling, the molecular structure of the coating is tight, and the machine has superior weather resistance. The coating manufacturer’s guarantee of the service life of the coating began to be ten years, 15 years to guarantee more than 20 years.
American research institutions have tested and compared fluorocarbon, super, and general coatings. The samples of the coatings were exposed to hot sunlight in Florida, the United States, and exposed to the harsh environment of humid salty air for 12 years, which proves that the stability and durability of fluorocarbon coatings are 30%-80% higher than those of the other two coatings. Fluorocarbon coatings ensure that they can be used in various harsh environments. It is especially suitable for indoor and outdoor decoration in public places, commercial chains, exhibition advertising, and other decorations and displays.
Color-coated aluminum coil production process
The production process of color-coated aluminum coil includes pretreatment, coating, drying and curing, quality inspection, and packaging. First, pretreatment is an essential step in production. The raw aluminum coil is cleaned, degreased, and passivated to remove oil, oxide, and other impurities on the surface and improve the adhesion of the coating. After pretreatment, the surface of the aluminum coil is smoother and flat, which lays a good foundation for the subsequent coating.
Next comes the coating process. According to customer needs, the appropriate paint and color are chosen, and the surface of the aluminum coil is evenly coated using professional coating equipment. During the coating process, the thickness and uniformity of the coating need to be strictly controlled to ensure its quality and appearance.
After coating, the aluminum coil enters the drying curing stage. The solvent in the coating evaporates by drying at high temperatures, and the resin solidifies, forming a solid and durable coating. The control of drying temperature and time has an essential effect on the coating performance and needs to be precisely adjusted according to the type and thickness of the coating.
Finally, qualified color-coated aluminum coil products will be sent to customers after quality inspection and packaging. The inspection process includes testing the coating thickness, color, gloss, and weather resistance to ensure the product’s quality meets the standard requirements. When packing, moisture-proof and scratch-proof packaging materials are used to ensure that the product is not damaged during transportation and storage.
main parameters of color-coated aluminum coil
- Base material thickness: The base material thickness of color-coated aluminum coil is usually between 0.2mm and 3.0mm, and different thicknesses of aluminum coils are suitable for different application scenarios. Thinner aluminum rolls are suitable for interior decoration, while thicker ones are more used in areas such as outdoor building curtain walls.
- Coating thickness: Coating thickness is an essential indicator of the quality of a coated aluminum coil. In general, the coating thickness is between 20μm and 70μm, and it is adjusted accordingly according to the use environment and requirements.
- Color and gloss: The appearance of color-coated aluminum rolls is rich and diverse, and the colors include a variety of monochrome, metallic colors and imitation wood grain, imitation stone grain, and other textures. The gloss can be customized according to the application scenario, ranging from matte to high gloss.
Characteristics of color-coated aluminum coil
- Machinability: color-coated aluminum coil has good plasticity and processing properties, and it can be processed into various shapes and sizes through shearing, bending, stamping, and other processes to meet different design needs.
- Corrosion resistance: The color-coated aluminum coil surface coating has excellent corrosion resistance, can resist erosion by acid, alkali, and other chemical substances, and extends service life.
- Weather tolerance: The color-coated aluminum coil is highly resistant to weather, can maintain color stability under various harsh climatic conditions, and does not quickly fade.
- Environmentally friendly: The color-coated aluminum coil is coated with an environmentally friendly coating, does not contain harmful substances, and meets environmental protection requirements. At the same time, the aluminum itself is recyclable, contributing to resource conservation and environmental protection.
- Good ornamental: Color-coated aluminum rolls offer more prosperous and better colors and textures. They can be customized for different occasions and styles to achieve different decorative effects.
Color-coated aluminum coil, as a rich color of high-performance, multi-functional new environmental protection aluminum. It has been widely used in building curtain walls, interior decoration, aluminum-plastic panels, aluminum louvers, composite panels, and aluminum ceilings for its excellent anti-corrosion and anti-rust ability, wear resistance, and excellent adhesion and flexibility. At the same time, because of its good color stability, outdoor durability, and weather resistance, color-coated aluminum coils in the industry, transportation, electronic products, packaging, and other fields also show a huge market potential.
Because of its rich color, corrosion resistance, fire resistance, and other characteristics, the color-coated aluminum coil is often used in the interior and exterior walls of buildings, ceilings, columns, foyers, and other places of decoration materials. Whether it is a residential building, a commercial super complex, or a large exhibition center, the rich color and texture of the coated aluminum roll can add color to the building and dress it up. Whether it is a multi-functional large building or a unique and creative new building, the machinability of color-coated aluminum coil can always meet the different requirements of modern and classical architectural styles, and improve the overall beauty of the building. The good plasticity and rich color of color-coated aluminum rolls provide architects, designers, and owners with personalized color spaces for exterior walls and ceilings, and it is the ideal material for various architectural forms.
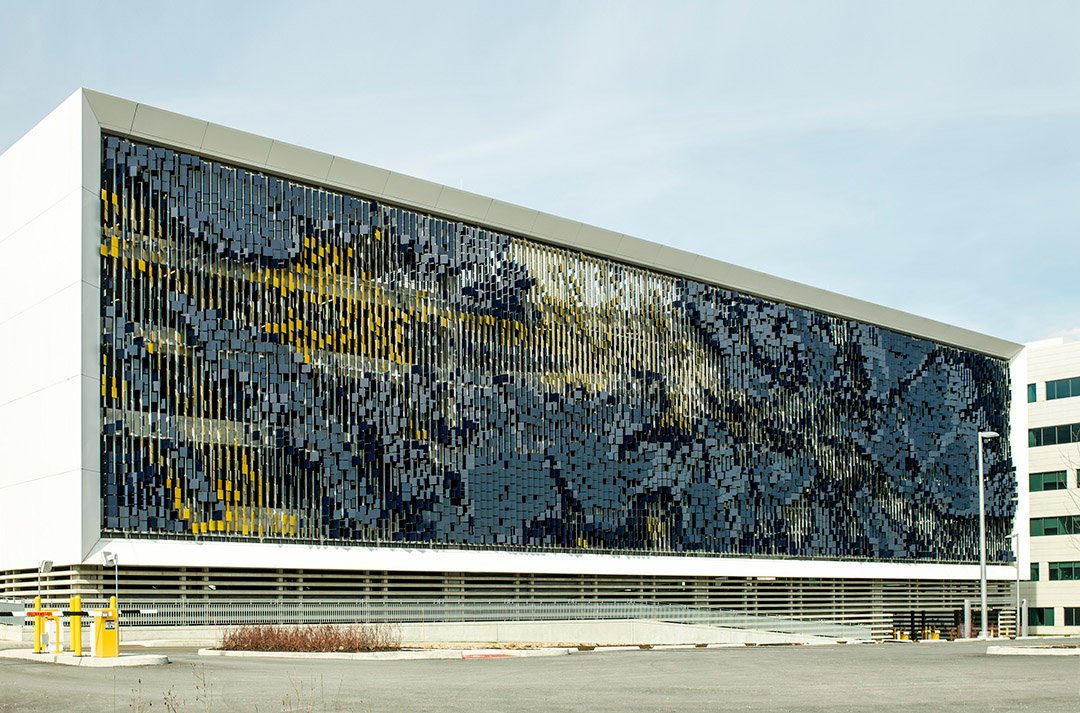
The Eskenazi Hospital parking lot in Indianapolis, USA, for example, uses 7,000 color-painted aluminum panels as decorative materials for its facade, which are connected through an articulated color system to create a dynamic facade system. The color-coated aluminum plate has excellent weather tolerance and UV resistance and can withstand the erosion of natural environments such as sunlight, rain, and wind for a long time. At the same time, it also has a rich choice of colors and can be customized according to the architectural design needs of different colors and patterns, and different perspectives of different colors, both pedestrians and drivers flow in the dynamic, making the whole building like a large public art. After several years of use, the exterior walls of the building still maintain bright colors and good decorative effects, proving the excellent performance of color-coated aluminum rolls in the field of architectural decoration. Color-coated aluminum coils have become an indispensable part of modern architecture.
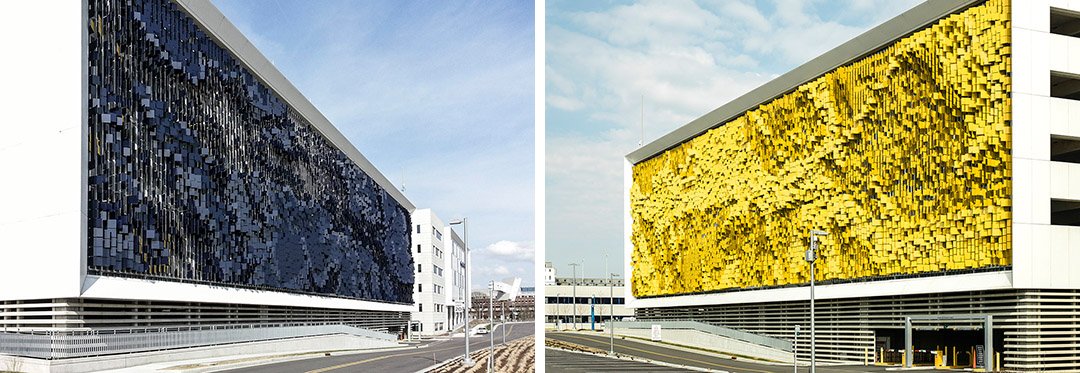
It can be used as a structural layer of the building curtain wall system, adding beauty and texture to the building. According to statistics, in recent years, the size of China’s color-coated aluminum market has been expanding year by year, with a total transaction value between 40 billion and 50 billion RMB, of which the construction and decoration field accounts for the largest proportion. In 2022, the national production of color-coated aluminum coils totaled 25.71 million tons, and the output of color-coated coils in China in 2022 was 27.63 million tons, an increase of 7.46% year-on-year. With the development of the construction market, the market size of the industry will continue to expand.
Besides, Color-coated aluminum coil is not only limited to the construction and industrial fields, it is also widely used in furniture manufacturing. For example, the surface of furniture such as TV cabinets, coffee tables, and bedside tables can be decorated with color-coated aluminum rolls, which are both beautiful and durable.
Color-coated aluminum rolls also play an important role in the field of packaging. It can be made into various forms of food, cosmetics, cans, and other packaging boxes to improve the quality and grade of products. According to the relevant data of the General Administration of Customs, the total export of coated plate belts in China from January to November 2023 totaled 5.983 million tons, an increase of 16.5% year-on-year. In 2024, it is expected that the export volume of the color-coated coil will reach about 6.3 million tons. It proves the wide application and market demand for color-coated aluminum coils in the packaging field. Above all, the painted aluminum coil with its excellent performance and diversification of application, modern construction, and industrial production, is an important material in electronic products and other fields. Whether it is in the exterior wall decoration of large commercial buildings, in the roof wall material of industrial plants, or the field of furniture manufacturing and electronic product shells, coated aluminum rolls play an important role.
Through the specific examples and scientific and credible data in the article, we can have a more in-depth understanding of the application value and market potential of color-coated aluminum coils. In the future, with the continuous progress of science and technology and people’s pursuit of a better life, the application of color-coated aluminum coil will surely show its unique charm in more fields, adding more color and charm to our living and working space. At the same time, with the improvement of environmental awareness and the promotion of sustainable development concepts, color-coated aluminum coil as an environmentally friendly material, market demand is also continuing to grow. More and more enterprises and projects began to choose color-coated aluminum coils as the preferred material to meet their requirements for beauty, durability, and environmental protection.
It should be noted that although color-coated aluminum coil has many advantages and a wide range of applications, it still needs to be selected and used according to specific needs and conditions in practical applications, and it is still necessary to pay attention to the correct installation and maintenance during use to ensure its long-term stable performance. At the same time, as consumers or users, when choosing color-coated aluminum rolls, they should also pay attention to the quality and brand reputation of the products to ensure the best use effect. I hope this introduction will give you a comprehensive and in-depth understanding of color-coated aluminum coils. Please consult our professional butler sales team for more information or data support.
Frequently Asked Questions
What makes WANTAI different
Over 15 Years of Experience
We have been working on aluminum alloy material processing for over 15 years. We know how to offer you professional butler service.
High-Performance Alloy Material
With our powerful DTC factory support, we can give you high-quality alloy material and the best price for your special requirements.
Lightning Butler Service
Your inquiry is critical in our daily work. Feel free to hit us. We focus on fast response to our customers’ business speed always.
Small Order Acceptable
We have thousands of tons of stock for various sizes and grades and small order quantities are acceptable.
Customized Size Acceptable
Customized size, width, and thickness are acceptable. Special requirements could also be negotiated.
Improving Always
Keep learning daily about the world’s newest developing alloy material research, material process machines, and ways.
Fast And Reliable Service For Your Project, We Do It All!
Professionally Experienced Butler Service Team Quick Response To Your Free Consulting